How Real-Time Inventory Management Transforms Appliance Repair Services
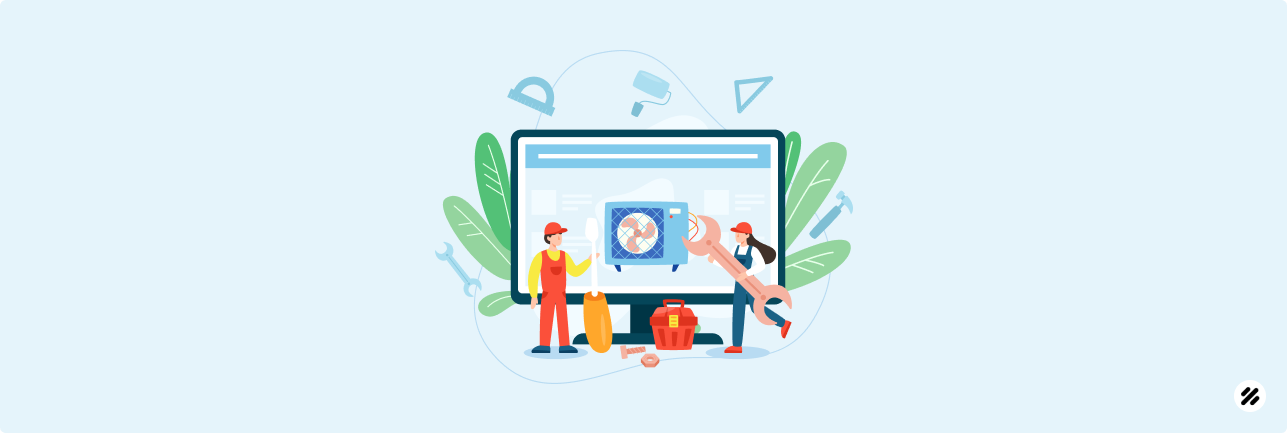
Appliance repair services, which are essential undertakings for any home appliance business often face the challenge of inefficient inventory management. This can lead to delays in repairs, customer dissatisfaction, and increased operational costs. Traditional inventory tracking methods, such as manual spreadsheets or outdated software, can be time-consuming, error-prone, and hinder overall efficiency. To solve this problem an automation tool (MFH). MyFieldHeroes can make your inventory management easy with real-time data. Let’s explore how real-time stock management can enhance your appliance repair service.
The Power of Real-Time Inventory Management
Real-time inventory management offers a transformative solution to these challenges. Using automation tools like MyFieldHeroes managers can get up-to-the-minute visibility into their stock levels. In other words, appliance repair businesses can gain unprecedented visibility into their stock levels, track parts usage, and optimize their operations. It’s because the tool acts as an excellent bridge between inventory managers and field staff.
Ways Real-Time Inventory Management using Field Automation Tools can Transform Service
1. Every Minute Updates
When you have MFH in hand you can get every minute update from your field technicians. Using the instant messaging feature, MFH enables technicians to quickly identify and locate the necessary parts, reducing downtime and improving customer satisfaction. This leads to quick service.
2. Cost-effectiveness
MFH can help minimize stockouts and excess inventory. When you know how much of each product you have in your hand, you can significantly reduce costs associated with purchasing, storage, and disposal.
3. Enhanced Decision-Making
Real-time data empowers managers to make informed decisions about inventory levels, purchasing strategies, and resource allocation. When managers have the tool in their hand they can connect with their inventory staff anytime. Even if the staff is present in locations with a weak internet connection, updates can be given in the portal.
Improved Customer Service
With accurate inventory information, technicians can provide more reliable repair estimates and reduce the likelihood of unexpected delays.
How Real-Time Inventory Management Works?
Let’s see
1. Real-Time Updates
Inventory levels are updated automatically in the portal as parts are used or received, ensuring accurate data. Any stock coming in or moving out is communicated to the managers using the automation tool.
2. Mobile Access
Using the automation tool, technicians in warehouses can access inventory information from their mobile devices, enabling them to check stock levels on-site and minimize delays.
3. Analytics and Reporting
Advanced analytics tools provide insights into inventory trends, usage patterns, and potential areas for optimization.
Final Thoughts
Real-time inventory management, powered by automation tools like MyFieldHeroes, offers a transformative solution for appliance repair businesses. By providing up-to-the-minute visibility into stock levels, tracking part usage, and optimizing operations, businesses can enhance efficiency, reduce costs, and improve customer satisfaction. The ability to access real-time data empowers managers to make informed decisions, streamline processes, and deliver exceptional service.
The FAQ’s
5 FAQs about Real-Time Inventory Management for Appliance Repair Services
FAQ 1. How does real-time inventory management help reduce operational costs?
- Minimizes stockouts and excess inventory: By having accurate and up-to-date information about stock levels, businesses can avoid unnecessary purchases and reduce the costs associated with storage and disposal of excess inventory.
- Optimizes purchasing decisions: Real-time data allows for more efficient purchasing strategies, ensuring that the right parts are ordered at the right time and in the right quantities, reducing costs and minimizing waste.
FAQ 2. What are the benefits of real-time inventory management for customer satisfaction?
- Reduced wait times: With accurate inventory information, technicians can provide more reliable repair estimates and minimize unexpected delays, leading to improved customer satisfaction.
- Increased reliability: Customers can have confidence in the business’s ability to complete repairs efficiently and effectively, as real-time inventory management helps ensure that the necessary parts are readily available.
FAQ 3. How does real-time inventory management improve decision-making?
- Data-driven insights: Real-time data provides valuable insights into inventory trends, usage patterns, and potential areas for optimization, allowing managers to make informed decisions about resource allocation, purchasing strategies, and overall business operations.
- Proactive problem-solving: By identifying potential issues early on, managers can take proactive steps to address them, such as adjusting inventory levels or optimizing repair processes.
FAQ 4. Can real-time inventory management be integrated with existing systems?
- Yes, most automation tools like MyFieldHeroes can be integrated with existing systems, such as accounting software or CRM platforms, to provide a seamless and efficient solution. This integration allows for better data synchronization and analysis.
FAQ 5. How does real-time inventory management ensure data security?
- Robust security measures: Automation tools typically employ advanced security features to protect sensitive data, such as encryption and access controls. This helps to safeguard inventory information and prevent unauthorized access.